A visual journey through the artistry and innovation behind watch dials…
You may not know this, but of all the parts of a watch, a dial requires the most manual work before it can be assembled. To better understand the importance of dial techniques and where they originated, this article guides you through the evolution of this fascinating art form.
The evolution of dial designs throughout history
When it comes to the world of horology, a beautifully finished movement is not enough. An exquisite timepiece should be intricately and meticulously decorated from the inside out. Matching the beauty of their ultra-precise complications, many watch brands choose traditional decorative techniques to execute their dials. These are called métiers d’art. The name means “art professions”. Many of the tools used for the craft, along with the know-how are passed down the family line or through apprenticeships.
The skills required for traditional watch dial decoration cannot be acquired overnight. They take several years to perfect and several hours of painstaking commitment to create. Any true watch aficionado will agree that maintaining these time-honoured techniques is integral to upholding the heritage of traditional Swiss watchmaking. Over the years, many techniques have been phased out, yet some prestigious manufacturers make it a commitment of theirs to keep this special art alive.
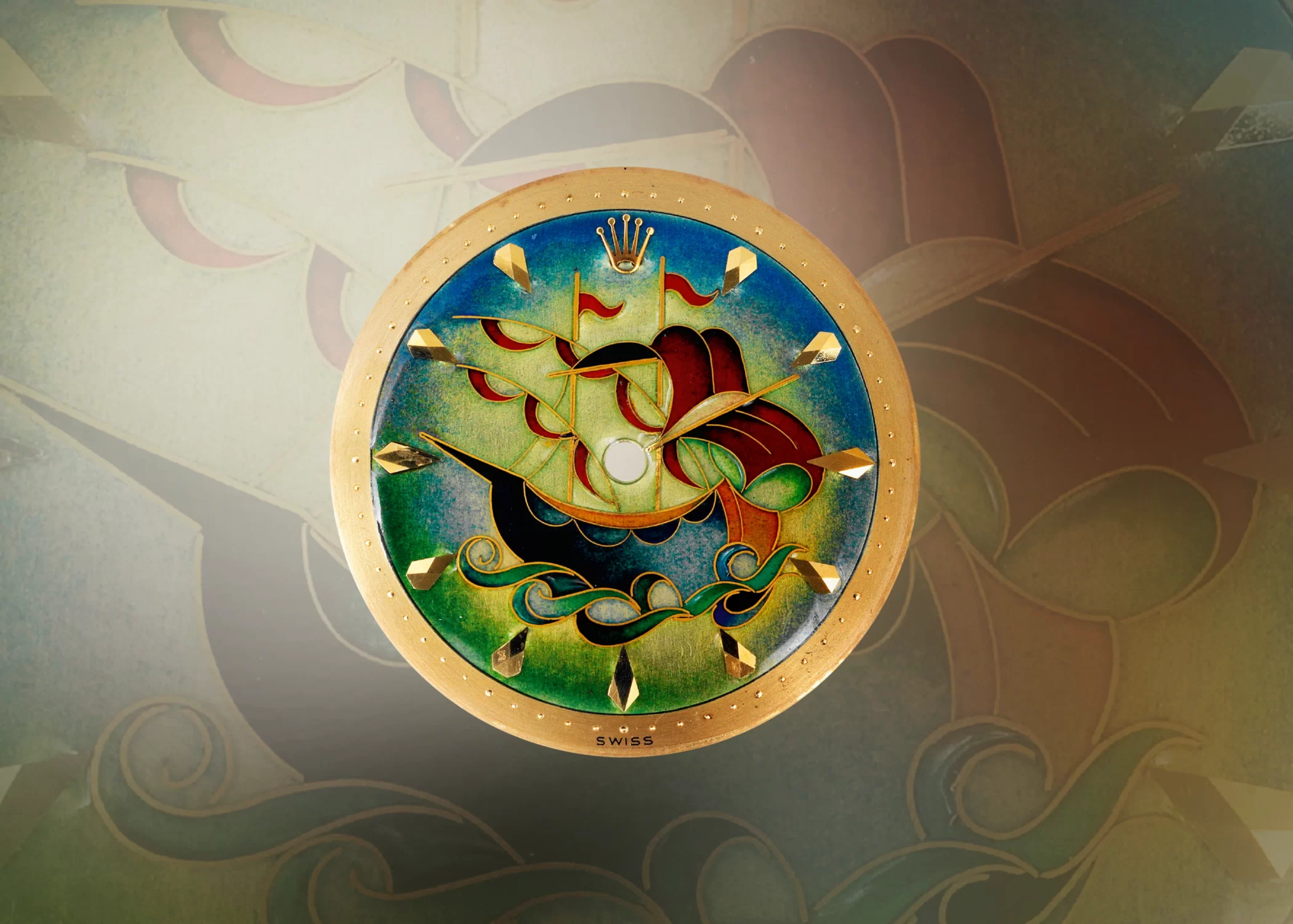
The artistry of hand-painted and decorated dials
Some examples of métiers d’art include engraving, enamelling and guilloche techniques. These special finishes lie at the intersection between human skill and engineering, forming an art that many collectors will pay considerably high prices for. The dial begins as a piece of metal that is shaped from brass, silver or another metal before decoration and colour are applied. These finishes add texture, structure and pattern to the dial. In some instances where machinery is not used and hand-applied decoration is undertaken, each timepiece is entirely unique to the wearer.
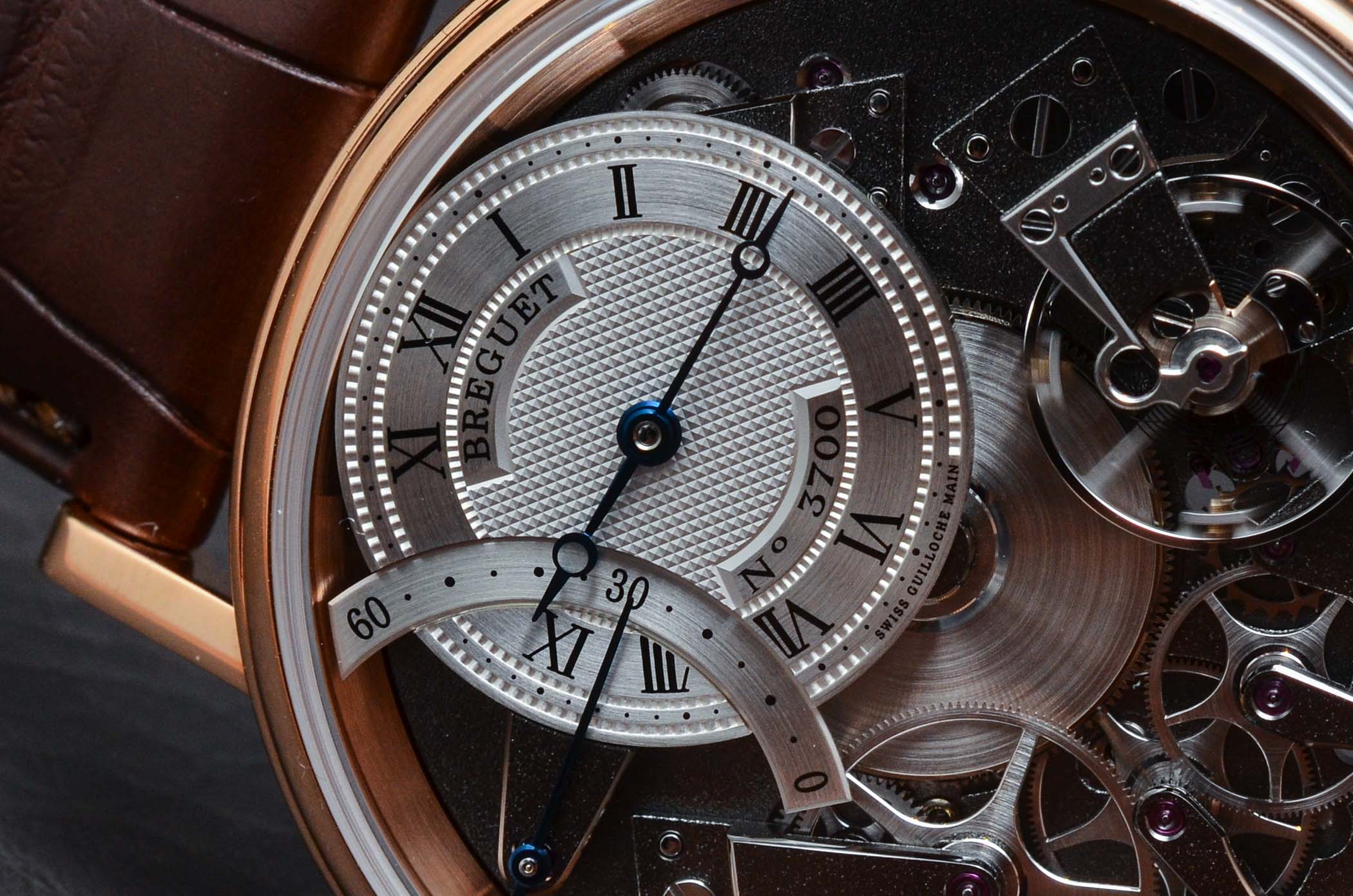
Engine turning (Guilloche)
Engine turning (otherwise known as guilloche) is a process that requires a sharp cutting tool to create geometric patterns on the surface of a dial. These carved patterns use a rose engine machine to create a precise finish such as basketweave, rosettes, or diamond “hobnail” effects. The technique dates as far back as the 16th century and was perfected by famed watchmaker, Abraham-Louis Breguet. Guilloche really became popular around the turn of the 20th century, however, during the advent of the Industrial Revolution. Vacheron Constantin watches from the 1930s and 1950s are great examples of timepieces that celebrate the beauty of guilloche dials during this time.
Although guilloche dials are considered the most common type of métiers d’art, they are by no means easy to create. The traditional machine is often controlled by an artisan, leaving no room for error. A slight slip of the machine and the entire dial is ruined. Some of the most popular guilloche dial types seen in modern watches today include the Tapisserie finish seen in the Royal Oak by Audemars Piguet, the Clous de Paris - a finish often used by experts at Maurice Lacroix - and the common sunburst effect. Other brands known for their exceptional work with guilloche dials include Girard-Perregaux, Patek Philippe, and Parmigiani Fleurier.
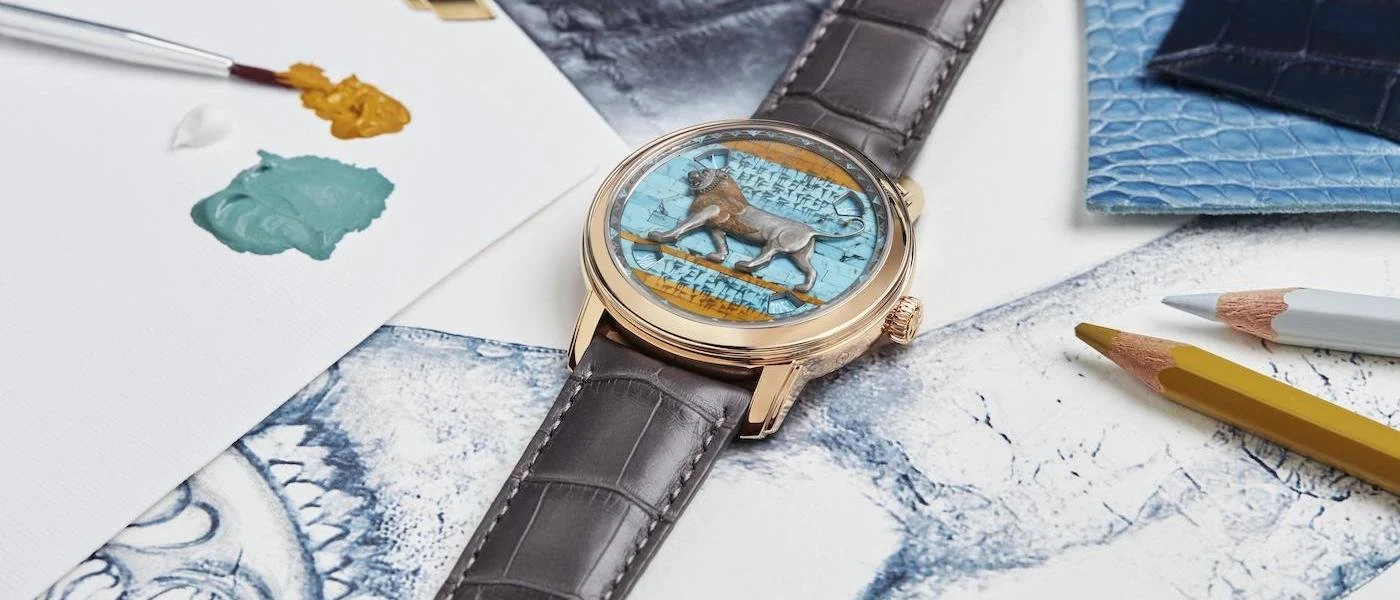
Engraving
Engraving is a technique that is commonly used as a form of métiers d’art. Often applied by hand, artisans decorate dials, along with cases and movement components, using different styles learned over the years. Some specialist tools are used to achieve these patterns, many of which are adopted by artisans at Vacheron Constantin like the bas-relief technique.
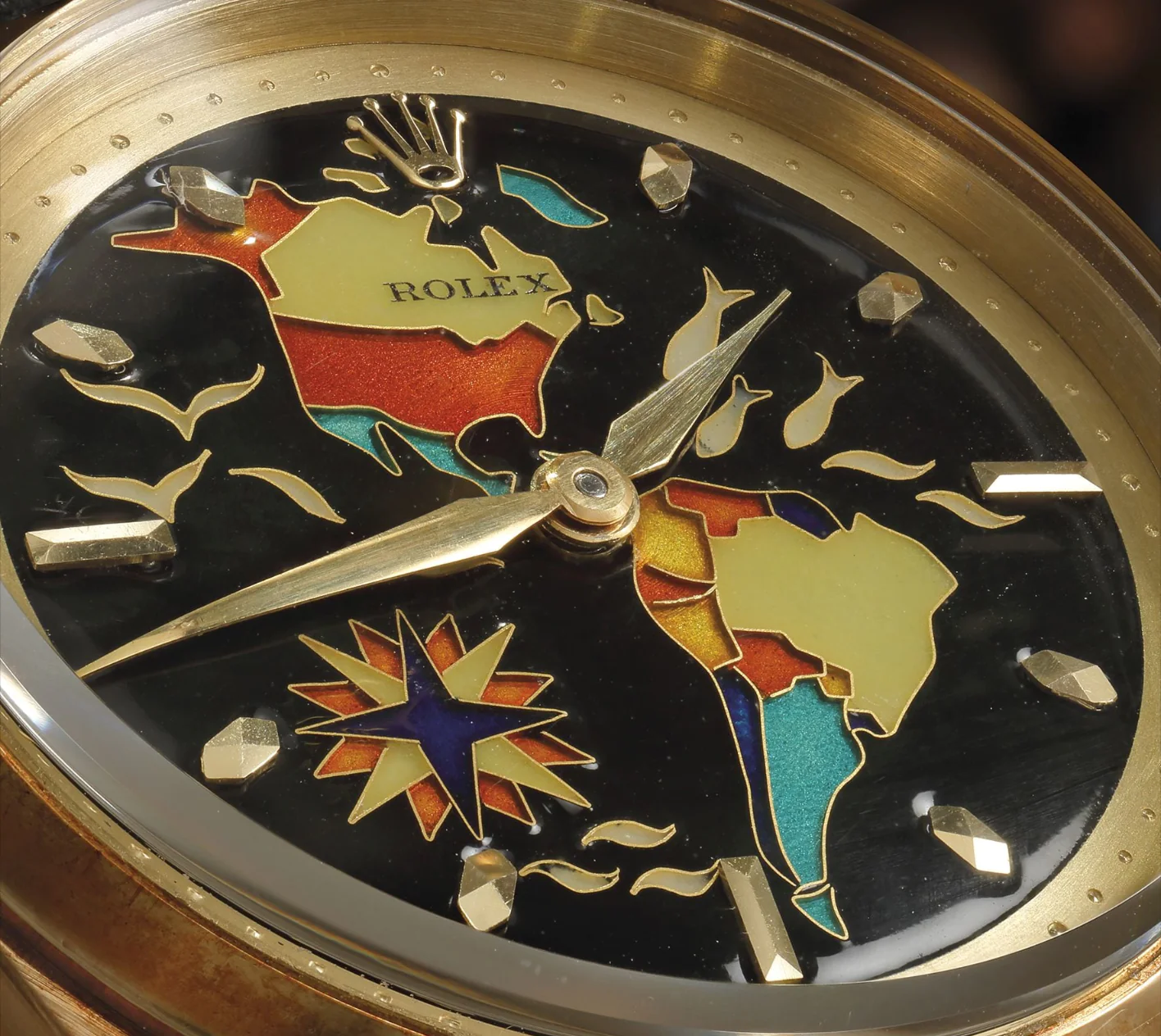
Enamelling
There are many forms of enamelling when it comes to creating watch dials. The process involves adding layers upon layers of coloured enamel to the surface of a dial. After each layer is applied, the dial is fired at extremely hot temperatures in a kiln, exposing it to the risk of cracking or becoming dull. It is one reason why this form of dial decoration is one of the most temperamental and risky of all. The fact that the colour of enamel changes when exposed to heat means that the artisan needs to compensate for this beforehand. A shade too light or too dark and the entire dial has gone to waste and the enameller must start the process again.
One example of enamelling is the cloissoné enamel, whereby artisans outline a motif using flat gold wire before filling the tiny sections with coloured enamel. Champlevé enamel is a process that combines enamel painting with engraving. A design is first etched into the watch dial, followed by a painted enamel finish. It gives the surface of the dial a three-dimensional effect.
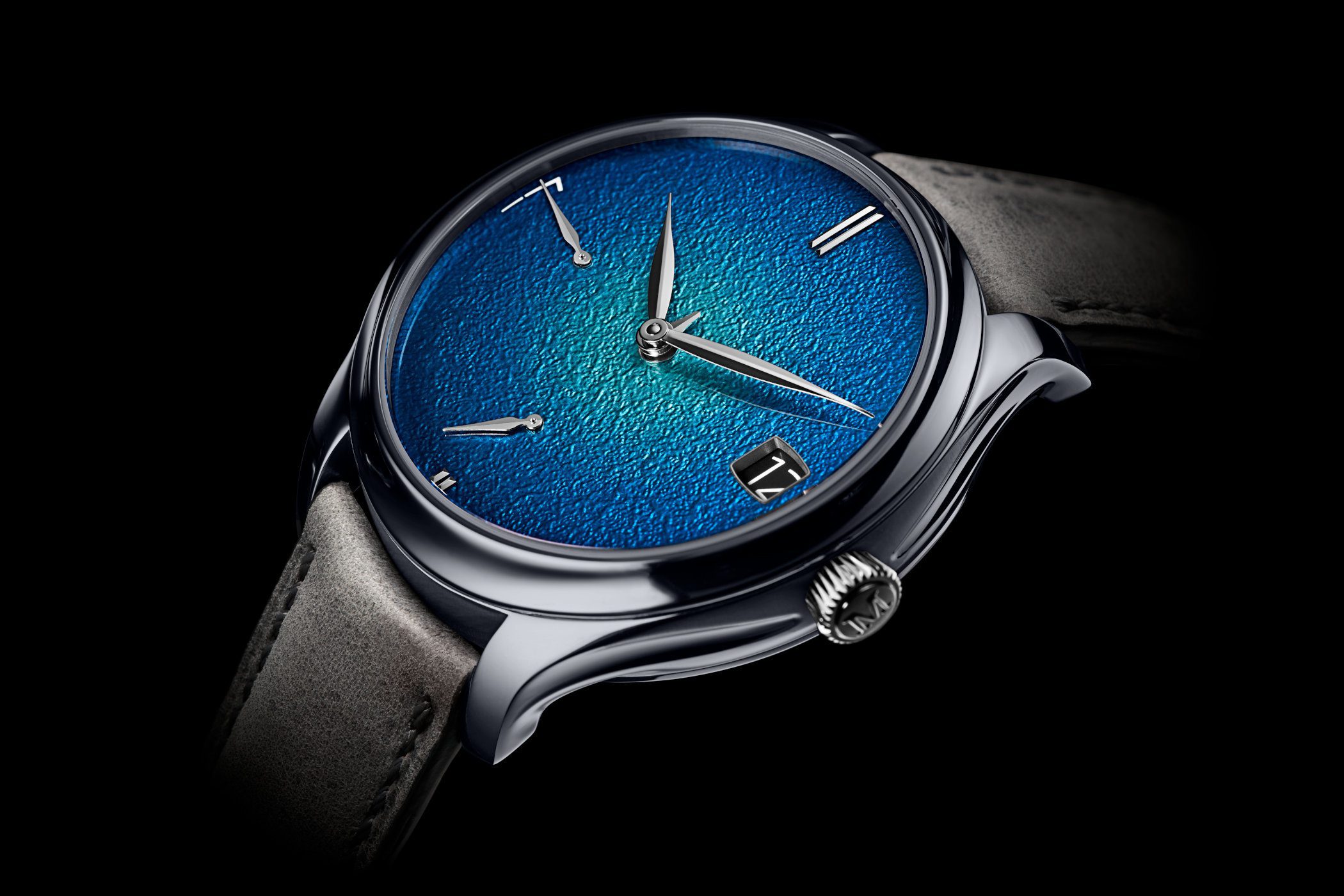
Plique-à-jour enamel is a rare form of enamelling, whereby a stained glass window effect is achieved. The enamel is fired in sections but creates a transparent effect along with a vivid, intense colour. Fume dials, on the other hand, can still be found in modern watches today, particularly those made by the likes of H. Moser & Cie and Louis Erard. They achieve a rich gradient effect. A dial begins as one colour (either at the bottom or in the middle) and spreads out into a darker or lighter shade. Gradient dials impact the look of a watch greatly, often enabling a wearer to enjoy a colourful dial that is less intense than a solid block of colour.
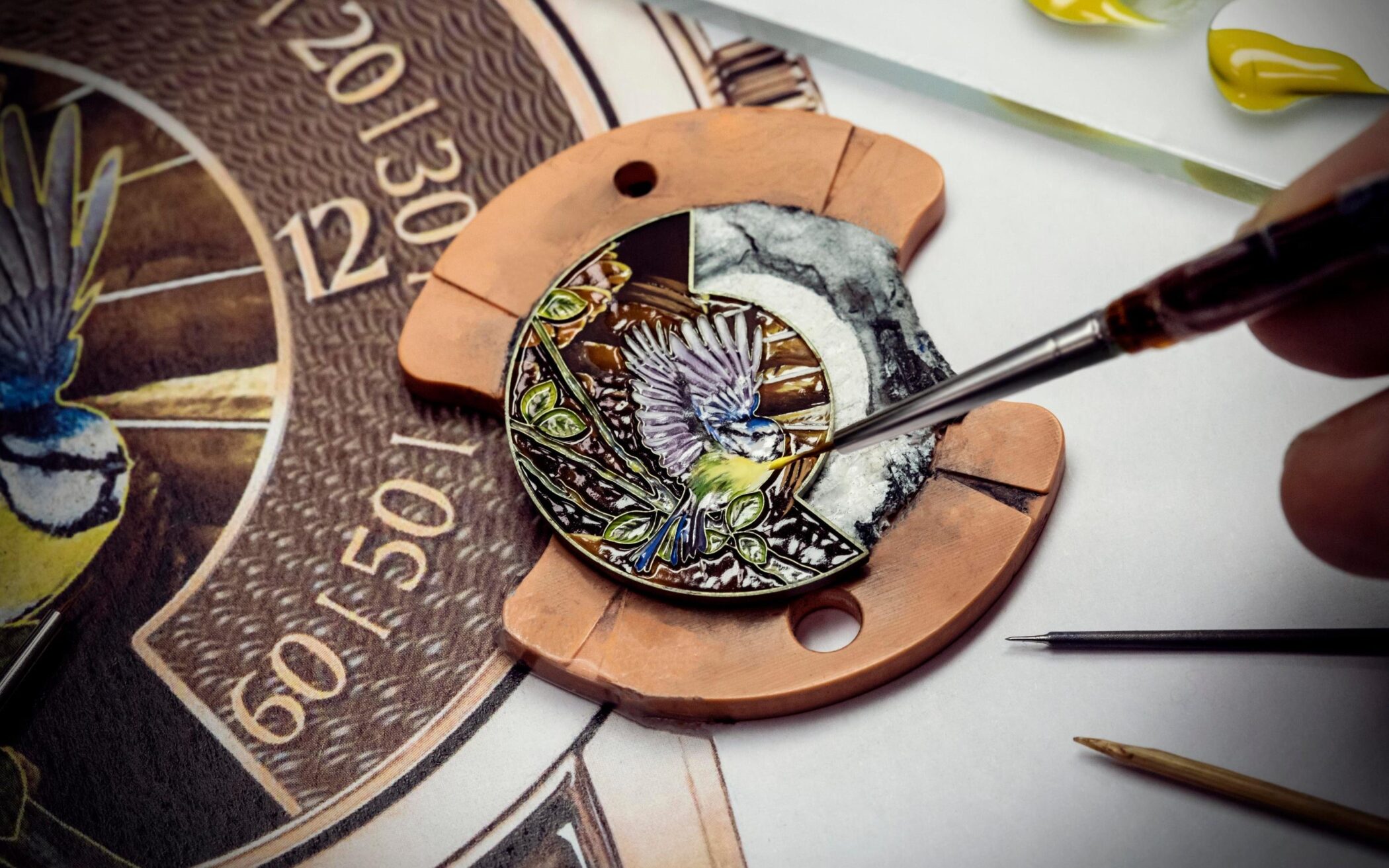
Miniature painting
Some artisans applying a hand-painted technique to an exquisite watch do so with extra fine brushes. Some of these consist of a single hair. This painstaking process is a testament to the dedication and determination of the skilled craftsman who carries it out. In some circumstances, the brushes themselves have been hand-made to suit each miniature painting.
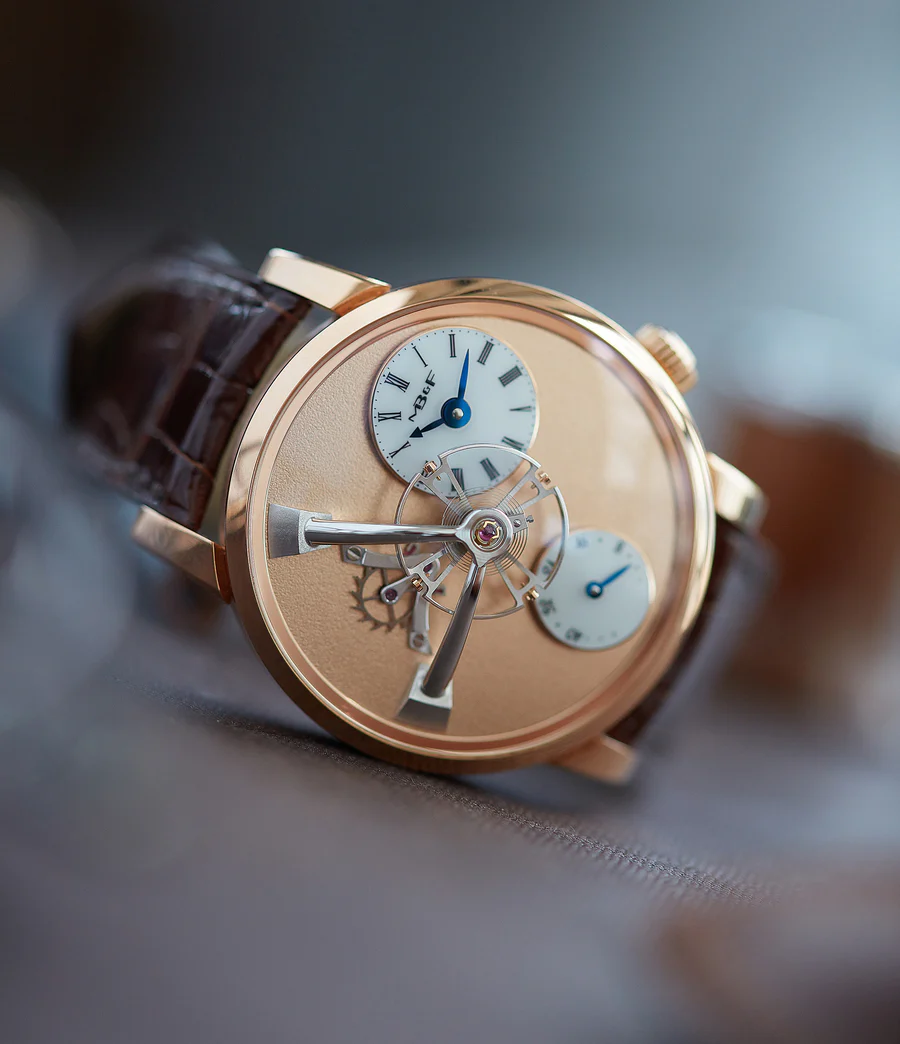
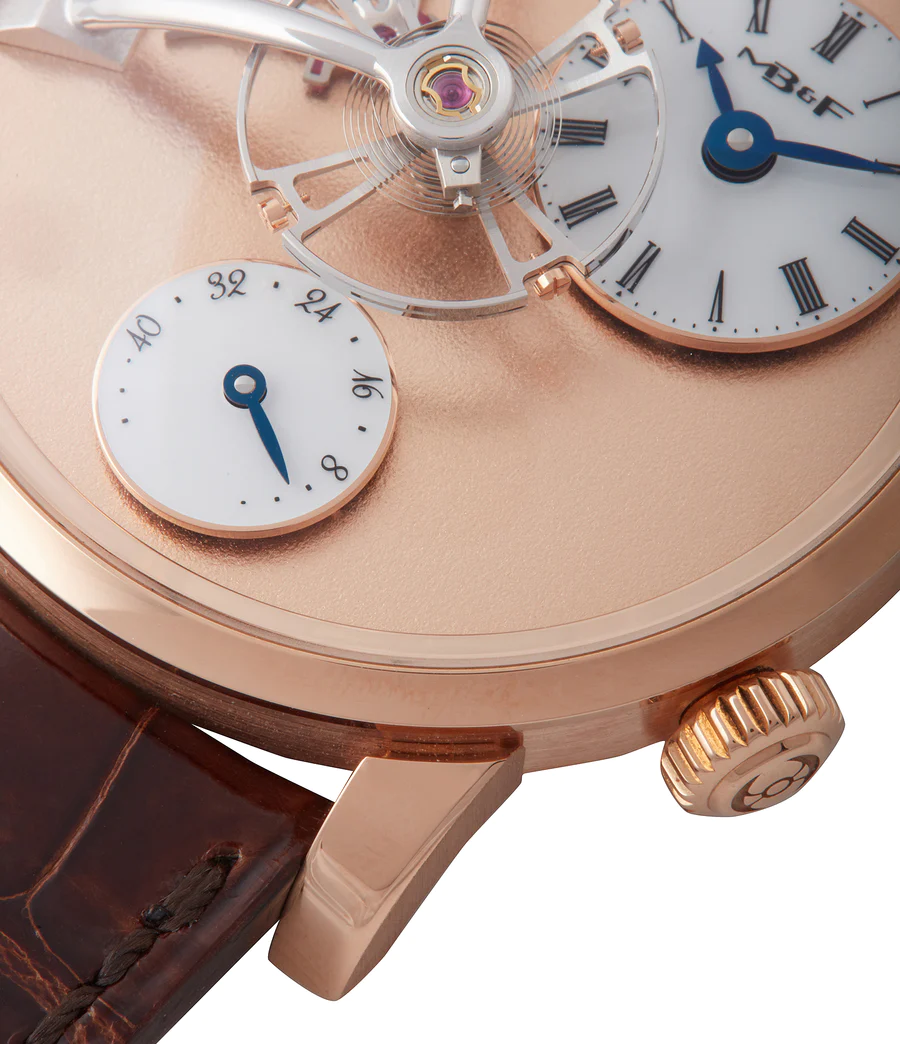
Frosting
Frosting is another dial technique that can be traced back to Abraham-Louis Breguet. The frosting effect would remove impurities from a silver dial through a heated process. This part of the method turns the dial black before the dial is treated with acid. The process is then repeated several times until a stunning silvery-white surface is achieved. The dial effect, reminiscent of a crisp winter frost, creates a unique finish. A similar effect can also be achieved via a wire brush.
Hand hammering
Hand hammering requires the skill of a steady hand, a hammer and a stake. The stake is tapped hundreds of times into the surface of the dial creating a textured surface that is completely different every time. One watchmaker alone creates this effect – each result unique to the craftsman. The human element of finishing a dial is a desired feature of a luxury timepiece for many connoisseurs. Irregularities in depth, spacing and randomness are not seen as impurities here. Moreover, they make the watch more desirable to a collector.
Most iconic dial makers
Over the years, some manufacturers have focused greatly on meticulous dial finishes. As such, they have become renowned, not only for their unmatched skills in this area of expertise but for their work in reviving ancient Swiss watchmaking techniques.
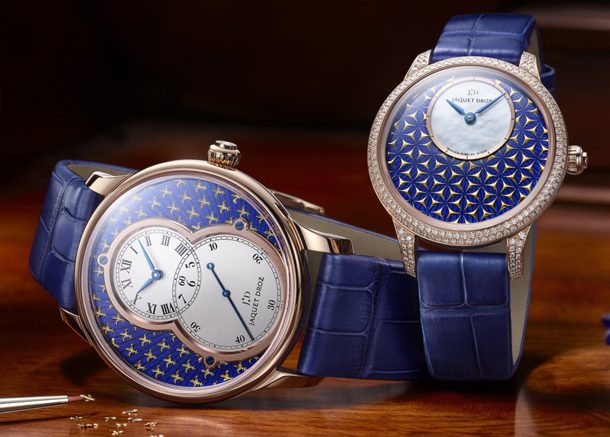
The Jaquet Droz Fleur de Lys and the Jaquet Droz Fleur de Vie watch are two examples in particular that capture the brand’s strong relationship with intricate dial decoration. Their paillonné enamelling dials uphold an artistic technique that dates back to over 300 years ago. The age-old decorative technique begins with guilloche work on a gold dial before it is covered in translucent coloured enamel to enable the guilloche pattern to shine through.
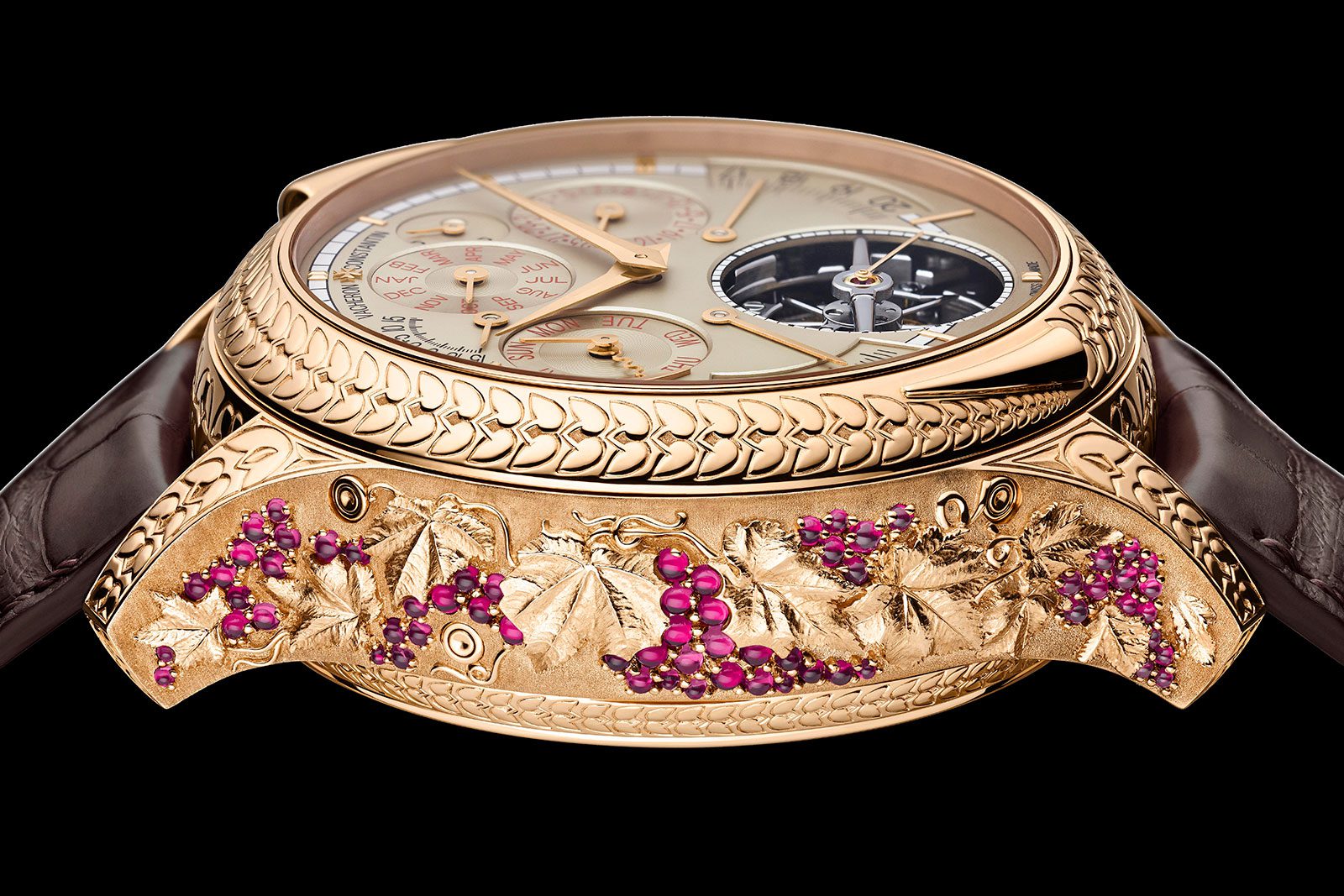
Vacheron Constantin is another superb example. It has produced watch dials executed in the Champlevé enamel technique and has intricately engraved solid gold watches like the Les Cabinotiers Grand Complication Bacchus watch. It features engraved leaf motifs, grapes and scintillating rubies. In recent years, the company’s special Les Cabinotiers workshop has even collaborated with the Musée de Louvre, auctioning off a hand-engraved and hand-painted watch from its Métiers d’Art collection.
Patek Philippe is a world-renowned expert at Cloissoné enamel – an execution that is shown off in its Jazz dome clock from the Rare Handcrafts collection. Other experts in decorative watch dials include H. Moser & Cie who has perfected the art of the fume dial, as well as Breguet with its many Clous de Paris guilloche dials, including the Classique Tourbillon Extra-Plat Anniversaire 5365.
Closing thoughts
The attention to detail required to create a beautifully decorated watch dial is a form of art. For many, keeping the traditional technique of dial decoration alive is of utmost importance. Although hand-applied finishes are less common today than they once were, métiers d’art in modern watchmaking form is still widely available with guilloche, engraved and enamelling finishings to choose from.